Rotary Index Laser Marking
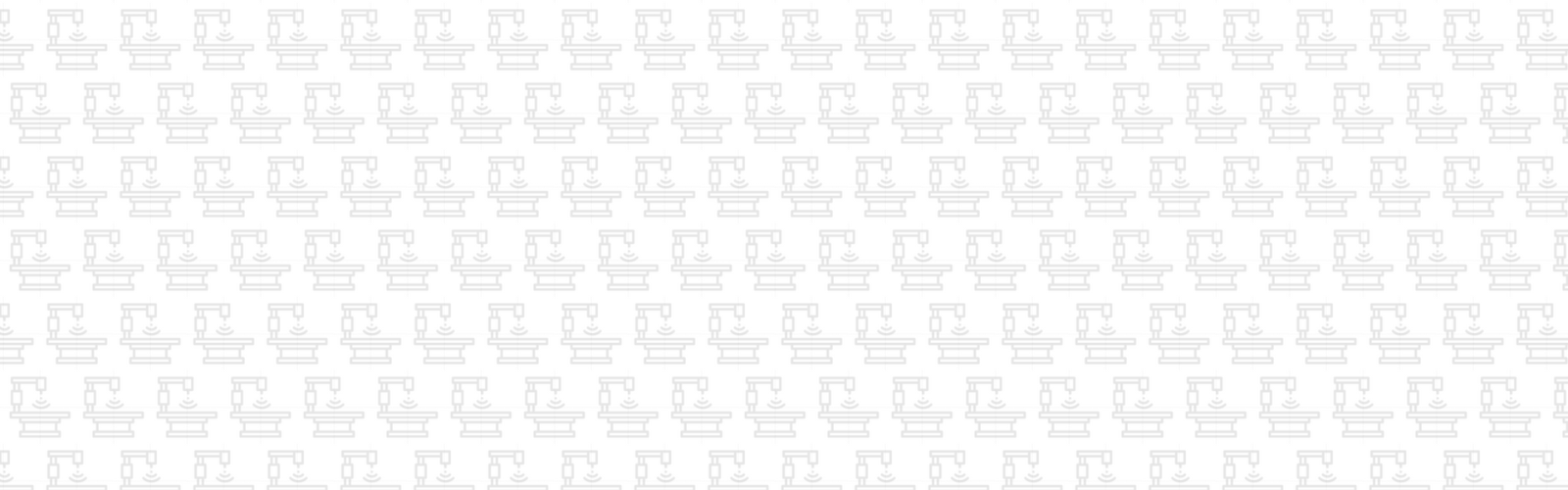
- Home
- Accessories
- Rotary Index Laser Marking
If a cylindrical-shaped object is placed under the focusing lens of a laser marker there is only one place on that object which is at the focal point of the lens. In steered beam (galvo-driven) laser marking systems, the lens can focus on a plane rather than a single spot. When one tries to laser mark around a cylindrical object the laser beam quickly goes out of focus as it wraps around the cylinder.
Either the lens's focus plane must be moved to keep the laser beam in focus or the marking on the cylinder must be limited to a section small enough to stay within the lens's focus capabilities. A third technique is to mark the cylinder with a bit map marking file and mark one line of pixels at a time.
Moving the focus plane of the lens in a galvo-driven system is referred to as 3D marking. It is generally done by passing the laser beam through a relay lens before it passes through the primary focusing lens. That relay lens is usually attached to a high-speed galvanometer.
If the marking job file has a 3D component to it then the relay lens can quickly change positions and cause the focal plane of the primary focusing lens to shift to accommodate the curvature of the cylindrical object. 3D marking is usually limited to about .5 inches of Z-axis change in the part.
An advantage of 3D marking is that it is very fast. However, it is limited to about .5 inches of Z-axis change and, at best, 160 degrees of marking around the cylinder. It also requires a marking file with a Z-axis component.
Marking small segments of the marking file requires that each marked segment remains within the focus capabilities of the focusing lens. This technique requires software capable of breaking the marking file into small segments and using laser marking settings that allow those segments to be joined seamlessly.
This technique is referred to as tiling. Tiling, when used with a proper rotary device, allows a part to be marked 360 degrees around its circumference.
Bit map image marking is inherently slow because it requires the rotary device to rotate the part for each line of pixels but it does have the advantage of being able to mark 360 degrees around the circumference of a cylinder.
Bit map image marking is rarely suitable for fiber lasers and frequently unsuitable for CO2 lasers because of the difficulty of getting overlapping pulses to control the quality of the mark on the part.
Jimani’s laser marking systems do not support either 3D marking or bit map image marking around cylindrical objects. Our approach has been to use vector image marking files that either handshake with a rotary indexer or break the image into individual segments and employ the tiling technique around the cylinder.
Both of those techniques are capable of marking 360 around a cylinder and are described below.
Rotary Indexers For Handshaking
A Sherline 8700 rotary indexer controller can communicate with either Leopardmark or Prolase software to perform rotary “handshaking”.
The Sherline Controller communicates with Leopardmark or Prolase software via a cable connecting the controller to the I/O communications port at the rear of the marking computer.
The rotary indexer is installed on a right-angle tilt plate, and the Sherline Manual X-Y Table has a threaded mating hole pattern to accept the tilt table mounting holes. A self-centering 3 inch opening 3 jaw chuck is attached to the rotary indexer.
Rotary Handshaking Explained
When a rotary indexer is used in either a Jimani Hybrid or Jimani Langolier Laser Marking System, Prolase or Leopardmark Laser Marking Software can “handshake” with the rotary directly.
If we simply handshake, then we use the hardware configuration complete from Sherline except for a communication cable provided by Jimani. That cable connects the Sherline controller to the laser via the RTC Control Board I/O port. The marking software job file then sends move commands to the Sherline controller telling it to rotate a predefined amount.
The Sherline rotary controller then signals back to the marker software, confirming that the part is in the new position for continued marking.
This configuration includes the Sherline controller and rotary table with an attached stepper motor. The rotary table and motor are mounted on a right-angle tilt plate installed on either end of a Sherline Manual X-Y Table. The Sherline controller is user-programmed for rotational direction and distance. Jimani provides the communication cable that allows MOVE commands and MOVE COMPLETE acknowledgments to pass between the controller and the marking software.
Example of Laser Marking Using Rotary Handshaking
Rotary for Tiling
DCA Rotary Tiling is designed for high-speed circumferential marking in applications that require marks around a cylindrical-shaped item. Prolase DCA Laser Marking Software is required for DCA Rotary Tiling.
Learn more about DCA Rotary Tiling.
The hardware consists of a rotary-encoded Clearpath servo motor mounted on a right-angle tilt plate. A Sherline 3-inch opening self-centering chuck is attached to the servo motor shaft. A motor power supply and a communication cable connecting the motor to the DCA Communication Port at the rear of the marking computer are included.
DCA Rotary Tiling has proven to be an ideal solution for marking products like the stainless thermal tumbler and glassware shown.
Since standard chuck jaws are not suitable for these types of products, Sherline designed replaceable chuck jaws in a joint development effort with Jimani for handling larger diameter parts.